HAZARDS IN IRON & STEEL INDUSTRY
Iron and steel industry is a heavy industry, involving a whole range of processes-chemical, metallurgical, mechanical, electrical, construction, road and rail traffic, materials handling, earth moving, nucleonic and many others. Each of these processes has many in-built hazards, falling broadly into three categories.

Ads by Oxado
MAGNET CRANES
The main stand of blooming mill presents a serious hazard in the form of red hot flying scales. Similarly, at 1000 ton shears, there have been incidences of metal splashes from molten cores of blooms. In these areas, if one does not remain very vigilant, one may get exposed to hazards from flying scales metal splashes.
INSTRUMENTATIONS AND PROCESS CONTROL
1. PROJECT AND CONSTRUCTION DIVISION
2. APPROACH TO HAZARD CONTROL
One basic approach to any hazard control has been that in the first place, the hazard to be controlled has to be controlled has to be identified. A typical “safety hazards and emergency steps” should be studied. Such studies are made shop-wise and process control sheets are prepared indicating the hazards involved. Safety measures required and the safety appliances needed norms are to be taken from those prescribed under the factories act and rules, environment, water and air pollution act and rules.
ABOUT TRAINING :
Merely having updated safety books is not enough If these are to be strictly followed, regular on the job training is essential for the operation on the machines and producer and for the employees in there respective trade. Employees have also to be trained before they are put on the job whenever there is a change of trade or transfer to another department. This is necessary to acquaint themselves fully with the hazards of the new trade and new work place.
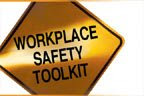
IRON AND STEEL IT HAS THREE ZONES :
Ø Raw materials storage, preparation and handling yard.
Ø Coke ovens and by-products plant.
Ø Sintering plant
Ø Blast furnaces.
Ø Gas holders and pipe lines.
2. STEEL ZONE COMPRISING OF -
Ø Steel melting shop
Ø Continuous casting shop
Ø Oxygen plant
Ø Slag and scrap yard
Ø Gas holders and pipelines
3. ROLLING MILLS ZONE COMPRISING OF -
Ø Different rolling mills,
Ø Gas booster stations and pipelines
Ø Loading bays for dispatch of finished materials
Ø Electrical cable tunnels and oil callers.